What is cable jacket?
The cable jacket serves as the protective outer layer of a cable, commonly manufactured from durable materials like PVC (polyvinyl chloride). This sheath encases the cable’s internal components—including conductors and insulation—to hold them securely together while providing essential physical protection. Without this outer barrier, the delicate interior elements would be left vulnerable to environmental and mechanical damage.
Exposure risks from an unjacketed cable include abrasion, moisture, oils, chemicals, extreme temperatures, and oxidation. These factors not only degrade electrical performance and reduce service life but also create significant safety hazards. Unprotected cables face higher risks of electrical leakage, short circuits, or even combustion due to compromised insulation integrity.
Proper jacketing is therefore mandatory for both functional and regulatory compliance. Manufacturers must select sheath materials specifically suited to the cable’s operating environment—whether industrial, automotive, or outdoor applications—to ensure long-term reliability while meeting safety standards. This makes the jacket a critical consideration in cable design and specification processes.
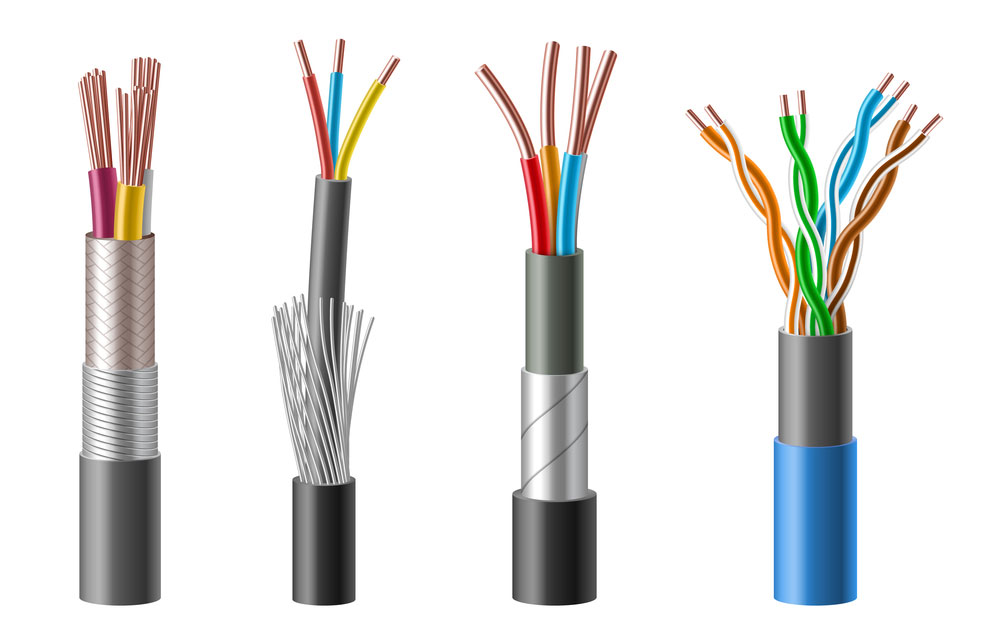
Common types of cable jacketing materials
1. Polyvinyl Chloride (PVC)
PVC is one of the most widely used cable jacketing materials due to its excellent balance of performance and affordability. It provides strong resistance to abrasion, moisture, and chemicals, making it suitable for general-purpose wiring in construction, appliances, and low-voltage applications. PVC is inherently flame-retardant, with many formulations meeting UL and IEC safety standards. Its flexibility across a broad temperature range (-20°C to 80°C) and the ability to be easily color-coded enhance its versatility in electrical installations.
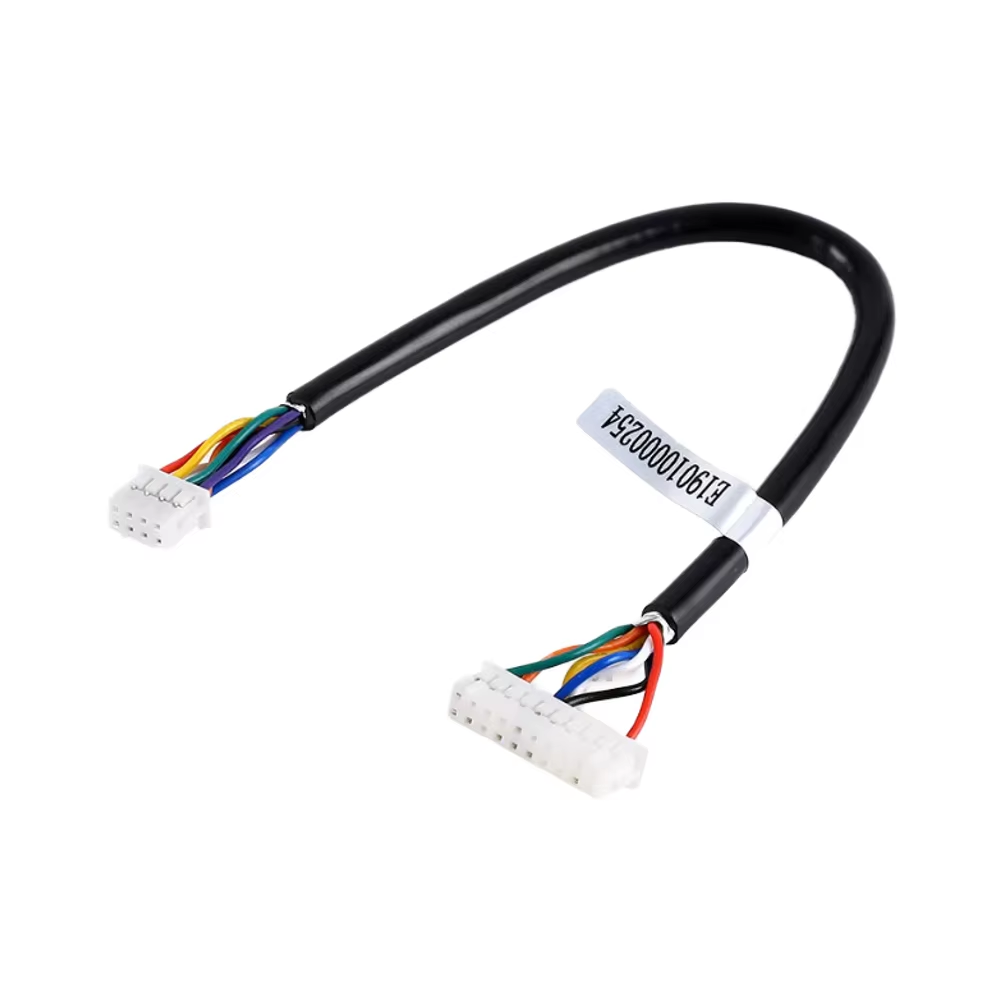
2. Polyurethane (PU)
Polyurethane stands out for its exceptional durability and flexibility, particularly in demanding environments. It offers superior abrasion resistance—5 to 10 times more than PVC—making it ideal for robotics, tow cables, and industrial machinery. PU maintains flexibility even at extremely low temperatures (-40°C) and resists oils, greases, and solvents, which is critical in automotive and hydraulic applications. Its ability to withstand repeated bending without cracking makes it a preferred choice for dynamic cable applications.
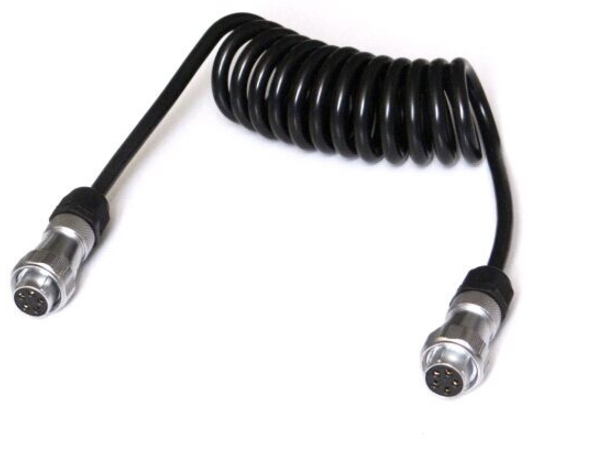
3. Rubber (EPDM, Neoprene, or CR)
Rubber jacketing, including EPDM, neoprene, and chloroprene (CR), excels in harsh outdoor and industrial settings. It provides excellent UV, ozone, and weather resistance, ensuring long-term performance in exposed environments. Rubber cables can endure high temperatures (up to 150°C for some grades) and remain flexible in cold conditions. Their natural vibration-damping properties make them well-suited for construction equipment, marine applications, and mining cables. Additionally, rubber offers strong electrical insulation and tear resistance, enhancing safety and longevity.
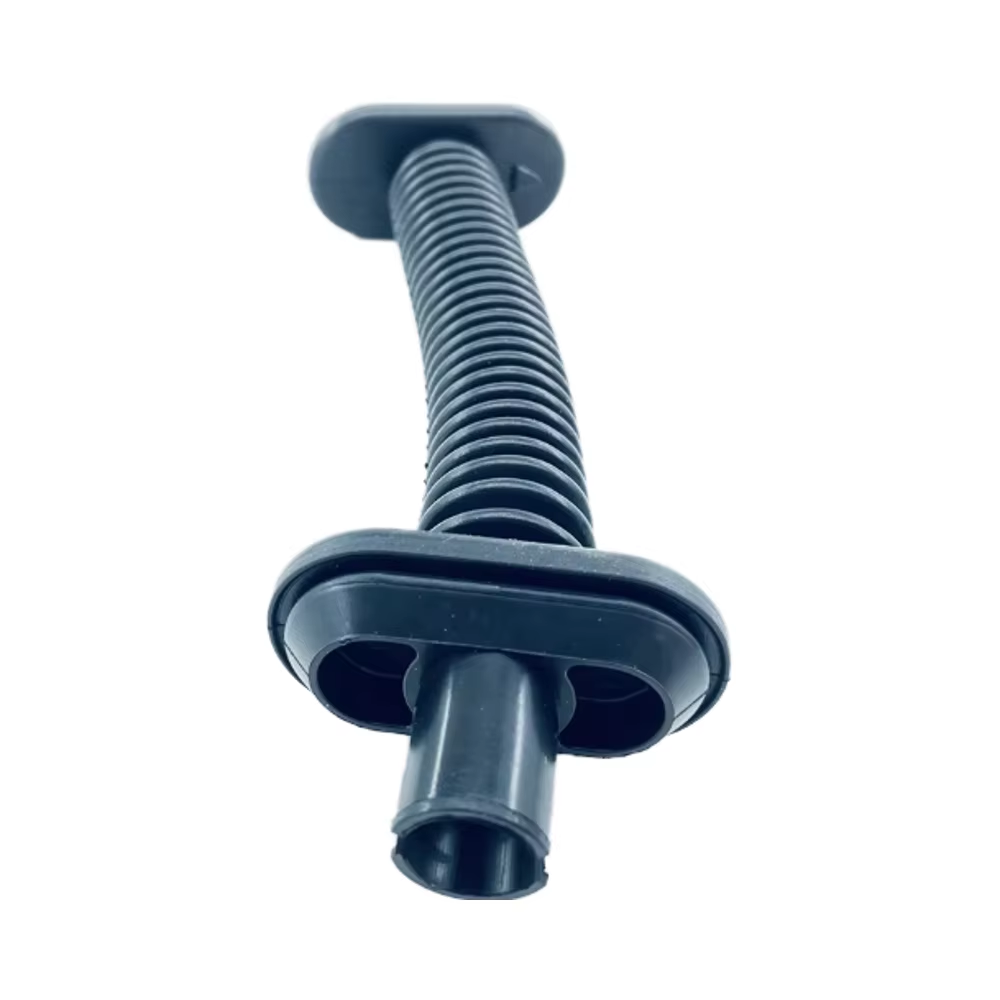
4. Silicone
Silicone is the go-to material for extreme temperature applications, with a working range of -60°C to 200°C. It is commonly used in high-heat environments such as industrial ovens, aerospace, and medical devices. Unlike many polymers, silicone remains flexible after prolonged exposure to heat and cold. It is also chemically inert, resisting oils, acids, and solvents, while its flame-retardant properties meet stringent safety standards. Additionally, its non-toxic nature makes it suitable for food-grade and medical applications.
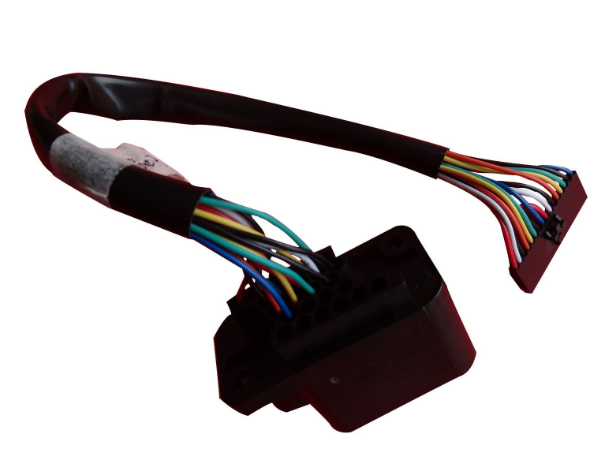
5. Nylon
Nylon is prized for its mechanical strength and thin yet tough protective qualities. It offers high tensile and impact resistance, making it ideal for Automotive Wiring Harnesses and connector backshells. Nylon’s ability to be extruded into thin walls allows for compact cable designs without sacrificing durability. It also provides excellent resistance to fuels and lubricants, a key requirement in transportation and industrial machinery. The smooth surface of nylon reduces friction during installation, while its fast extrusion process lowers manufacturing costs.
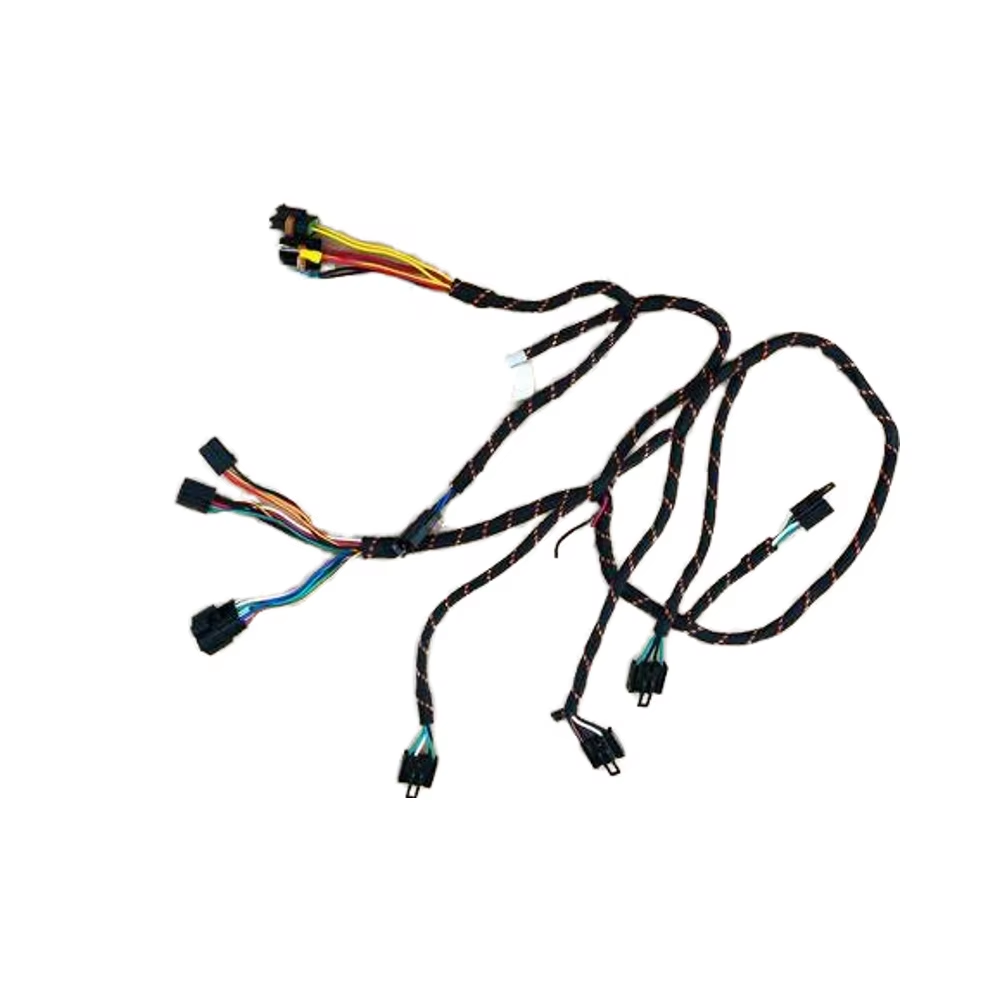
Benefits of Cable Jackets
1. Physical Protection
The jacket acts as a protective shield, safeguarding the cable’s internal conductors and insulation from mechanical damage. It prevents abrasion, crushing, cuts, and other physical stresses that could compromise the cable’s integrity. Additionally, it serves as a barrier against moisture, chemicals, dust, and other contaminants, reducing the risk of corrosion and short circuits. This ensures consistent signal transmission and power delivery in demanding applications.
2. Environmental Resistance
Cable jackets are designed to withstand harsh environmental conditions, including exposure to UV radiation, extreme temperatures, oils, and solvents. UV-resistant formulations prevent degradation in outdoor applications, while specialized materials maintain flexibility in both freezing cold and high-heat environments. This adaptability allows cables to perform reliably in industrial, automotive, marine, and outdoor installations.
Conclusion
The cable jacket serves as a critical protective barrier that safeguards the internal components of cables while ensuring reliable performance in various operating conditions. As the outermost layer, it provides essential mechanical protection against abrasion, crushing, and physical damage while simultaneously shielding conductors from environmental threats like moisture, chemicals, UV radiation, and extreme temperatures. Beyond physical protection, the jacket enhances electrical safety by improving insulation properties to prevent current leakage and signal interference.