Led Wiring Harness is a wiring assembly used to connect LED lamps, power systems and control modules. It consists of a variety of different types of wires, terminals, connectors, and sheath materials, and can provide efficient and reliable power and signal transmission in various lighting applications. LED wiring harnesses are usually customized according to the power, voltage, current, control requirements, etc. of LED equipment to ensure stable operation and convenient installation in complex environments.
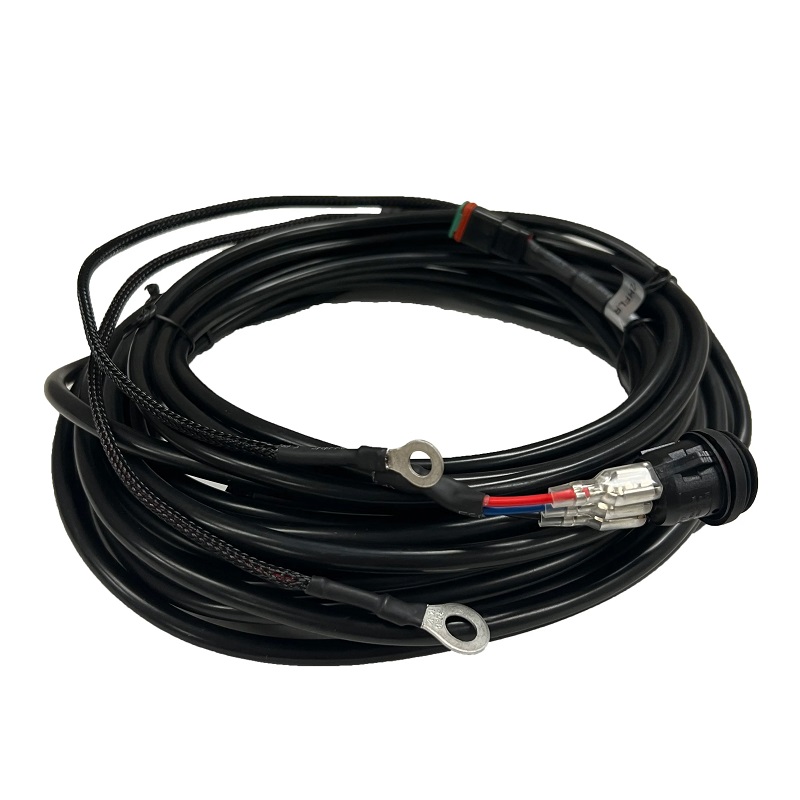
Applications:
Automotive lighting system: power supply and signal connection for LED headlights, taillights, daytime running lights, interior lighting and other parts.
Outdoor lighting projects: LED street lights, tunnel lights, square lights, park lights, floodlights and other scenes that require waterproof connections.
LED display system: such as full-color LED large screens, billboards, traffic lights, etc., rely on wiring harnesses to connect power supply and control modules.
Industrial and mechanical lighting: LED work lights, indicator lights, panel lights, etc. on mechanical equipment, wiring harnesses are used for complex wiring directions.
Home and commercial LED lamps: including internal circuit connections such as LED downlights, spotlights, ceiling lights, light strips, cabinet lights, etc.
Solar lighting system: connect solar panels, LED lamps, batteries and control systems to ensure stable operation.
Material:
Conductor material: mainly bare copper or tinned copper, with excellent conductivity, low resistance and strong reliability.
Insulation layer: different grades of plastic materials such as PVC, TPE, XLPE, silicone are used to provide temperature resistance, flame retardancy and moisture resistance.
Sheath material: the outer layer is wrapped with PVC sheath, nylon braided mesh or corrugated tube to improve wear resistance, UV resistance and oil resistance.
Connector and terminal: commonly used connectors such as Molex, JST, AMP, waterproof plugs, etc., and the terminals are made of tinned copper or brass.
Auxiliary materials: such as heat shrink tubing, cable ties, and electrical tape are used to fix and protect the wiring harness structure.
Features:
High customization flexibility: the wiring harness can be flexibly designed with wire length, color, interface type, etc. according to the structure of the lamp and circuit requirements.
High heat resistance and flame retardancy: in compliance with UL, CSA and other standards, the temperature resistance can reach above 105°C, ensuring stable operation under high temperature.
Waterproof and dustproof structure: using IP65 or higher protection connectors, suitable for outdoor or humid environments.
Compact and reasonable layout: unified wiring and connection integration, convenient for internal structure optimization and rapid assembly of lamps.
Excellent conductivity: using high-purity copper conductors to ensure low power loss and improve LED lighting efficiency.
Environmentally friendly and non-toxic materials: passing ROHS and other environmental standards, suitable for sensitive fields such as home, medical, and children's lighting.
Strong anti-interference performance: shielded cable structure can be provided for PWM dimming, signal synchronization and other scenarios to prevent signal interference.
Advantages:
Improve assembly efficiency: standardized connectors and modular structure facilitate rapid assembly of assembly lines, greatly shortening assembly time.
Improve stability and safety: insulation protection structure and firm terminal design to avoid hidden dangers such as short circuit and loosening.
Easy maintenance: the connector structure is easy to disassemble, which is convenient for later maintenance, replacement or upgrade of the system.
Support mass production and personalized customization: The factory can customize according to customer drawings and prototypes, and support small batch proofing and large batch orders.
Applicable to a variety of voltage and current levels: Covering common LED power supply standards such as 5V, 12V, 24V, 36V, and supporting high-power drive applications.
Strong environmental adaptability: Suitable for harsh industrial and outdoor environments such as high humidity, high temperature, and strong vibration.
Low technical threshold and easy integration: The entire LED system wiring is completed in advance by the manufacturer, and the terminal only needs to be quickly plugged in for use.
FAQ:
Can Led Wiring Harness be used directly outdoors?
Yes. LED wiring harnesses for outdoor use must adopt a waterproof design (such as IP65/IP67) and use UV-resistant, low-temperature-resistant and flame-retardant materials. The connector must have a sealing structure to prevent water vapor intrusion. Manufacturers can customize it according to the use environment to ensure its long-term and reliable operation.
Can LED wiring harnesses be adapted to all LED lamps?
Not completely universal. There are differences in power, voltage, pin definition, control method (such as dimming, RGB), etc. of different LED lamps. Exclusive wiring harness design is required according to the circuit board design, installation space, control signal, etc. of the specific lamp. Customers can provide samples or drawings for customization by suppliers.
Is the LED wiring harness easy to age? How long is the service life?
High-quality LED wiring harnesses are made of heat-resistant, weather-resistant, and anti-aging materials. They can generally be used for 5-10 years in indoor environments and can operate stably for 3-5 years in harsh outdoor environments. The service life also depends on factors such as installation method, current size, and temperature conditions.
How much current can the LED wiring harness carry?
This depends on the cross-sectional area and material of the selected wire. For example, a 0.5mm² copper wire can carry about 3-5A current, while a 1.5mm² copper wire can carry 10-13A current. The wiring harness design needs to be calculated based on the actual current load of the LED device and the operating temperature environment to ensure a safety margin.
How to test whether the quality of an LED wiring harness is qualified?
Quality inspection includes: appearance inspection (no cracks, indentations, or skew), continuity test (confirming no open circuit or short circuit), insulation test (checking for leakage risk), tension test (connection strength), temperature resistance and flame retardancy test, etc. Qualified wiring harnesses should provide relevant inspection reports and certification certificates.